
The -900 was designed to compete with the B777-200ER/LR and 787-10, and eventually giving airlines the option to replace their older A340-300/500 with a newer and more fuel-efficient aircraft.Cathay Pacific Airways has ordered 30 A350 XWB long range aircraft. The A350-900 has a maximum range of 8,100 (15,000 km) and a MTOW of 280 tons. The A350 XWB is Airbus newest aircraft.
(Picture © Airbus.) GKN Aerospace's rear spar for the A350 XWB demonstrator wing. The trials was designed to evaluate acoustic properties and to help fine-tune sound insulation for the A350 XWB cabin. The 15 m² structure was fitted in place of an existing A340 aluminium fuselage section. (Picture © Airbus.) In September, Airbus flight tested an A350 XWB fuselage panel made from CFRP. Lindner.) The A350 XWB’s advanced cockpit features six large LCD screens that represent the latest in display technology. (Picture © Airbus S.A.S.) The second test composite fuselage section for the A350 XWB was completed in Hamburg, Germany, in 2009.
Forward door - 285 cm x 168 cm (110 in x 66 in) Aft door - 280 cm x 168 cm (112 in x 69 in)aircraft-design fuel range airbus-a350. 64.8 m (212 ft) Hold door sizes. 7,642 miles (12,300 km) Engines.
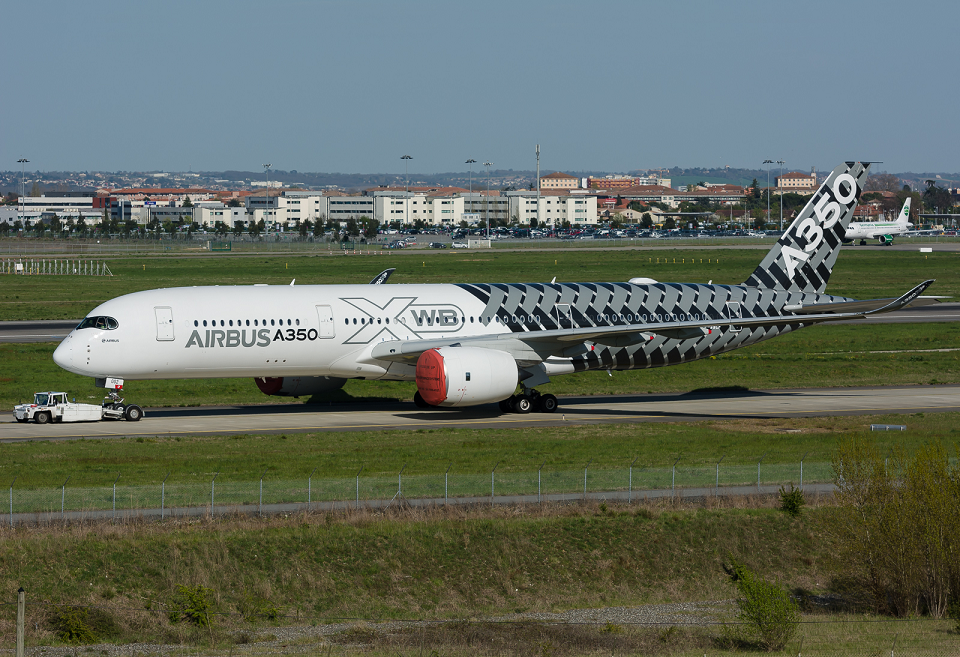
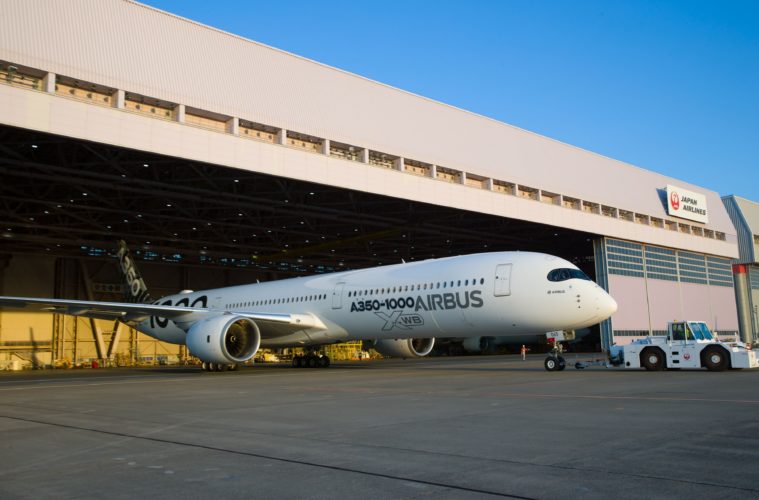
Although the A350 programme is facing delays of its own, so far these are of the order of months rather than years. Although low-weight metal solutions, primarily aluminium/lithium alloy and metal/composite hybrids such as GLARE, were considered, composites won out because of the prospects for greater integration, fewer parts and fasteners, lower maintenance and, it seems, the favourable attitude of airlines to the precedent set by Boeing.Paradoxically, the European planemaker gains from not being the leader in this particular airframe race since it can learn much from the problems experienced by Boeing that have led to a likely three-year delay in first deliveries of B787s. Admittedly, Airbus might still have preferred to maintain its more incremental approach to composites adoption but, goaded by its competitor, it is now fully committed to the plastic fuselage revolution. It now has extensive experience of reinforced plastics fabrication and service behaviour, while composites engineers on the A350 programme benefit also from the 15% plastic content in the Airbus A380 ‘superjumbo’. For a start, while Boeing has had to make a large jump from barely 10% composites content in its B777 airliner to the B787’s 50% figure, Airbus was an early composites adopter and has gained expertise while progressively adding fairings, nacelles, empennages, control surfaces and wings to its composite structures portfolio. Composites advantageAirbus believes it has advantages in the composites arena.
Intensive developmentAn intensive development effort has achieved significant milestones. The variants will share a largely common wing design and wing span though the -1000 model will have a 4% larger wing area, achieved by extending the trailing section aft. All A350s will have a range in excess of 8,000 nautical miles. The aircraft was conceived as an A330/340 replacement and will compete with larger variants of Boeing’s new B787 and its existing B777 long-range widebody twin.
Airbus has assembled a detailed digital model of the aircraft for use as a common reference for component manufacture by its own sites and its suppliers. The Maturity A milestone, which encompasses MG5 and earlier gates, was followed last year by Maturity B, by which point all design teams had finalised their designs.Today the A350 XWB is progressing steadily from the design and development phase towards production. Airbus regularly updates its data to these suppliers and many of the required tools are now available. This is crucial in the case of composites, for which production requires early commitments to tool manufacturers. MG5 cleared the way for detailed design of components and enabled production of jigs and tooling to commence for long-lead items.
Other benefits include easier handling, less expensive autoclaves and the fact that having a panel fail at post-manufacture inspection for any reason is less of a setback than losing a complete barrel. This less radical solution reduces risk, says Airbus, while also having the advantage that panel properties can be optimised to their locations in the fuselage (whether crown, belly or sides) with resultant weight saving. Whereas Boeing is producing the B787 fuselage in large monolithic tape-wound barrel sections that are subsequently joined, Airbus has opted to clothe a pre-fabricated fuselage skeleton with large carbon fibre composite panels. It has not gone quite as far down the dispersed outsourcing track as Boeing first aimed to do and, by maintaining closer supervision within its partnership arrangements, hopes to avoid the supply chain pitfalls that have afflicted the Dreamliner programme.The biggest difference in approach between the airframers, however, is that related to fuselage manufacture. A350 programme head Didier Evrard describes this activity as an essential ‘bridge between the digital model and the real world,’ important for validating composite production processes as manufacture ramps up towards the 10 aircraft per month rate targeted.A modified production strategy for the A350 sees Airbus relying on a select group of Tier 1 supplier/partners chosen for their ability to shoulder full responsibility for delivering large pre-assemblies that are complete and ready for assembly into the final aircraft.
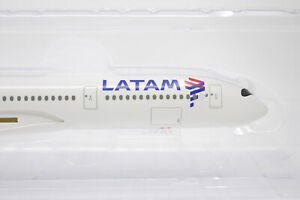
A €150 million fuselage assembly hangar at Hamburg, with a production area of some 15 000 m 2, was completed this summer. Final assembly of the aircraft will take place in Toulouse, France.Many of the production facilities, including those for composites, are new. Tailplane (empennage) components are being produced by Airbus Spain and Germany, and in China. However, Spirit AeroSystems is responsible for the wing fixed leading edge including the front wing spar, a 105 ft long composite structure weighing some 2000 lb.
A new composite production facility at Stade currently has a workforce of about 100, but this is expected to grow to nearer 500 as production builds up to full rate.
